Metal etching is an important manufacturing process, which is widely used in electronics, communications, automobiles, medical and other fields. This article will introduce the advantages and processes of metal etching in detail.
Advantages of metal etching
High precision and high efficiency
Metal etching can achieve high-precision and high-efficiency production through computer control. The use of advanced CNC machine tools and machining centers can accurately control the machining process to ensure that the parts produced have the characteristics of high precision and high efficiency.
Complex shapes and structures can be processed
Metal etching can process various complex shapes and structures, such as micro-small parts, thin plate parts, three-dimensional curved surface parts, etc. This makes metal etching have great advantages in manufacturing difficult and demanding parts.
Environmental protection and energy saving
The emission of pollutants such as waste liquid and waste gas generated during the metal etching process is very small, and the materials used can also be recycled and reused. This makes metal etching an environmentally friendly and energy-saving manufacturing process.
Reduce manufacturing costs
Metal etching can reduce manufacturing costs through mass production, and it can also reduce the number of molds and tools, thereby reducing production costs.
Process of metal etching processing
Preliminary preparation
In the preliminary preparation stage, raw materials such as stainless steel, copper, aluminum and other metal materials need to be prepared. At the same time, the raw materials need to be cleaned and dried to ensure that they will not be contaminated during the processing.
Design pattern
In the process of metal etching, the pattern needs to be designed first to facilitate the subsequent processing. The design pattern can be designed using CAD software or hand-drawn.
Lamination
The designed pattern needs to be transferred to the metal surface, a process called lamination. When laminating, a specific film or dry film is required to transfer the pattern to the metal surface.
Corrosion
Corrosion treatment is required after lamination. This process is to dissolve the part of the metal surface that is not protected by the film through a chemical reaction, thereby forming parts of the desired shape and structure. Commonly used corrosive agents include acidic corrosive agents and alkaline corrosive agents. The specific type of corrosive agent to be used needs to be determined based on factors such as the type of metal to be processed and the usage scenario.
De-filming and cleaning
De-filming and cleaning are required after corrosion is completed. Defilming is to remove the film attached to the metal surface with chemical reagents or mechanical methods for subsequent processing or use. Cleaning is to remove the residue and dirt on the metal surface to ensure the quality and safety of the product.
Post-processing
The post-processing stage includes product quality inspection, surface treatment, rust prevention, etc. Quality inspection mainly checks the size, shape, surface quality, etc. of the product to ensure that it meets the design requirements and relevant standards. Surface treatment is mainly to improve the appearance quality and corrosion resistance of the product, and can be treated by spraying paint, chrome plating, oxidation and other processes. Rust prevention is mainly to prevent the product from being corroded during use, and can be treated by applying anti-rust oil, spraying anti-rust paint and other methods.
In short, hardware etching processing has the advantages of high precision, high efficiency, processing of complex shapes and structures, environmental protection and energy saving, and reduced manufacturing costs, and is widely used in various fields. Its process includes preliminary preparation, design pattern, lamination, corrosion, film removal and cleaning, and post-processing. Each stage has its specific operating procedures and precautions, which need to be strictly controlled to ensure product quality.
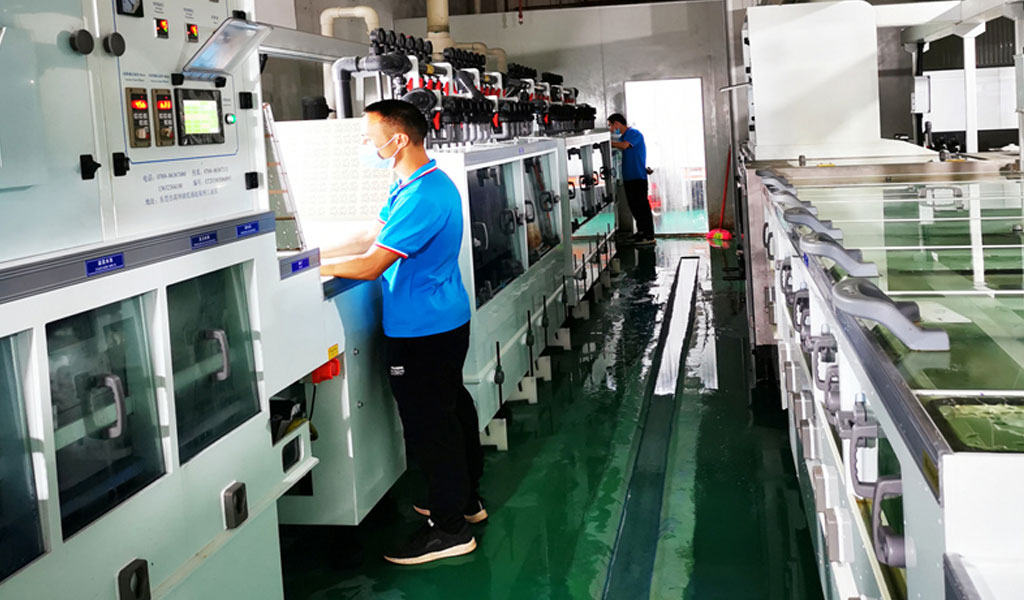
We Can Take Care Of Your Metal Etching Needs.
BE-CU metal etching china company’s strength lies in our investment in chemical etching production line. Chemical etching production line are the foremost innovation to the metal etching industry.
The programmability of Chemical etching production line gives us quick and accurate repeatability. This constant replication allows for better finishes, tighter tolerances and most importantly – faster cycles for metal forming.
By engaging our etching company, you can also get the much-needed support to design your part for any specific purpose. Our team can provide custom design tips, such as ensuring consistent wall thickness and avoiding overly thick sections that can sink.
Are you designing new products for projects companies? We can help! Here at BE-CU Metal Etching China Company, we offer a reasonably priced rapid metal etching service that will allow you to make an amazing prototype that will impress your clients. Get a free project review here so we can get started for your metal etching products!
- Photo Etching for Medical Use
- Photo Etching for Metal Sign
- Photo Etching for Jewelry
- Ferric Chloride Etching Stainless Steel
- The Best Acid for Etching Steel
- The Principle And Process Flow Of PCB Etching Machine
- In The Localization Of Wafer Foundry Equipment, Etching Machines Stand Out
- How Important is the Blind Hole Rate of Filter Screens?
- The whole process of stainless steel sheet etching
- What is the Role of Aperture Diaphragms in the Field of Optics?